The aerospace industry is continuously pushing the boundaries of lightweight, high-performance materials to improve fuel efficiency, durability, and electronic functionality. From electromagnetic interference (EMI) shielding to customized sensor housings and lightweight conductive enclosures, 3D printing with conductive filaments is becoming an essential tool for modern aircraft and spacecraft development.
At ABC3D, we provide advanced conductive filaments designed for high-strength, low-weight, and electrically conductive aerospace applications. By integrating 3D-printed conductive components, manufacturers can reduce material weight, optimize electronic performance, and improve aircraft safety without the constraints of traditional manufacturing.
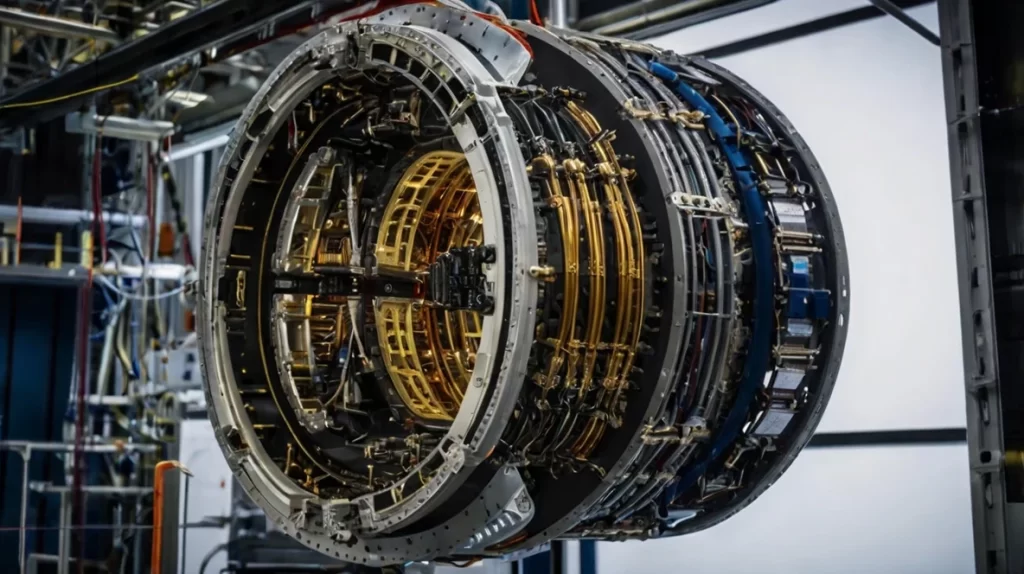
How Conductive 3D Printing is Revolutionizing Aerospace Components
Aerospace components require materials that balance mechanical strength, lightweight properties, and high electrical performance. Traditional methods for producing electronic enclosures, EMI shielding, and custom sensor components rely on machined aluminum, copper, or carbon fiber composites, which add weight and require costly precision machining.
With 3D printing and conductive filaments, aerospace engineers can:
- Reduce weight by replacing heavy metal shielding and enclosures with conductive polymer-based alternatives.
- Integrate conductive features directly into components, minimizing assembly complexity and external wiring.
- Prototype functional aerospace electronics faster and more affordably, without relying on expensive and time-consuming CNC machining.
These advantages allow for the creation of optimized, custom aerospace components with improved electromagnetic performance, weight efficiency, and adaptability to extreme conditions.
Key Aerospace Applications of 3D-Printed Conductive Filaments
From aircraft avionics enclosures to spacecraft shielding solutions, 3D-printed conductive parts are redefining how lightweight, functional aerospace components are developed.
1. EMI Shielding for Avionics & Communication Systems
Aircraft and spacecraft electronics generate electromagnetic interference (EMI), which can disrupt navigation, communication, and onboard sensors. Traditionally, EMI shielding requires metallic enclosures or conductive coatings, increasing weight and manufacturing costs.
With conductive 3D printing, manufacturers can:
- Print conductive enclosures for flight electronics, reducing the need for heavy metal shielding.
- Create integrated EMI-shielding layers within sensor casings, optimizing performance while minimizing weight.
- Design custom-fit avionics shielding components without the cost and time associated with CNC machining.
By using ABC3D’s carbon-loaded conductive filaments, aerospace manufacturers can effectively block EMI interference while maintaining low-weight, high-strength enclosures.
2. Lightweight Conductive Parts for Satellites & UAVs
Weight reduction is a top priority in aerospace design, where even a small decrease in mass can lead to fuel savings, extended range, and lower launch costs. 3D-printed conductive filaments offer:
- Lightweight, functional antenna housings and RF shielding components for satellites.
- Custom-printed conductive circuit paths for unmanned aerial vehicle (UAV) electronics.
- Hybrid thermoplastic composite parts that combine mechanical strength with electrical functionality.
By utilizing conductive polymer-based components, satellite manufacturers and UAV engineers can develop custom, low-weight solutions that enhance electronic performance while reducing overall mass.
3. Aerospace Sensor Housings & Custom Electronic Enclosures
Modern aircraft and spacecraft rely on embedded sensors for temperature monitoring, structural integrity assessment, and navigation systems. 3D printing with conductive filaments enables:
- Customized sensor housings with integrated conductive pathways, eliminating external wiring.
- Printed capacitive touch interfaces for cockpit controls, enhancing pilot-system interaction.
- Low-weight, ESD-safe enclosures for delicate aerospace electronics, protecting sensitive circuits from electrostatic discharge.
By using ABC3D’s high-performance conductive materials, aerospace manufacturers can develop more compact, efficient, and protective sensor enclosures without adding unnecessary weight or complexity.
Optimizing Conductive Filament Printing for Aerospace Applications
To maximize the performance, weight reduction, and electrical efficiency of 3D-printed aerospace components, it’s essential to fine-tune printing parameters and select the right conductive materials.
Best Practices for Conductive Filament 3D Printing in Aerospace:
- Select the Right Conductive Filament for Specific Applications:
- For EMI shielding and enclosures: Use carbon-loaded conductive ABS or polycarbonate.
- For flexible aerospace wiring applications: Use conductive TPU filaments.
- For high-strength, impact-resistant parts: Choose graphene-infused conductive filaments.
- Optimize Print Settings for Weight Reduction & Performance:
- Extrusion Temperature: Maintain 220-250°C for optimal layer adhesion and conductivity.
- Print Speed: Use 30-40 mm/s for precise deposition of conductive material.
- Layer Height & Infill: Lower layer heights (~0.1 mm) improve surface finish, while optimized infill structures reduce weight without sacrificing durability.
- Post-Processing for Enhanced Conductivity & Strength:
- Apply conductive coatings to increase electrical efficiency in EMI shielding applications.
- Use low-temperature soldering or conductive adhesives to improve connectivity with external circuits.
By integrating these techniques, aerospace manufacturers can maximize the weight savings, electrical performance, and mechanical reliability of 3D-printed conductive components.
Why ABC3D’s Conductive Filaments Are the Best Choice for Aerospace Applications
At ABC3D, we develop specialized conductive filaments tailored for aerospace-grade durability, conductivity, and lightweight performance. Our materials provide:
- Superior EMI shielding and electrostatic protection, ensuring safe, interference-free avionics.
- High-strength, impact-resistant formulations, ideal for spacecraft and aircraft component manufacturing.
- Lightweight alternatives to traditional metal shielding, reducing overall aircraft weight while maintaining electrical conductivity.
By using ABC3D’s advanced conductive filaments, aerospace manufacturers can develop next-generation, cost-effective, and lightweight electronic solutions for aircraft, satellites, and UAVs.
The Future of 3D-Printed Conductive Aerospace Components
As aerospace technology advances, 3D-printed conductive filaments will continue to play a major role in the development of lightweight, high-performance electronic components. Future innovations in multi-material conductive printing, graphene-infused aerospace composites, and self-healing EMI shielding will further push the boundaries of aerospace manufacturing.
custom aerospace electronics
Explore our range of aerospace-grade conductive filaments today! Need help selecting the best material for your project? Contact our team for expert recommendations and technical support!