In industrial manufacturing, machine reliability, efficiency, and customization are critical for maintaining productivity and reducing downtime. However, traditional methods for repairing, upgrading, or enhancing industrial equipment often require custom-machined parts, long lead times, and expensive outsourcing. The emergence of 3D printing with conductive filaments is revolutionizing how manufacturers approach machine maintenance, automation system enhancements, and custom upgrades, enabling on-demand production of functional, electrically conductive components.At ABC3D, we specialize in industrial-grade conductive filaments designed for machine repairs, custom automation components, and electrical upgrades. Our high-strength, electrically conductive materials allow manufacturers to fabricate replacement parts, integrate smart sensors, and improve factory automation systems, all while cutting costs and reducing machine downtime.
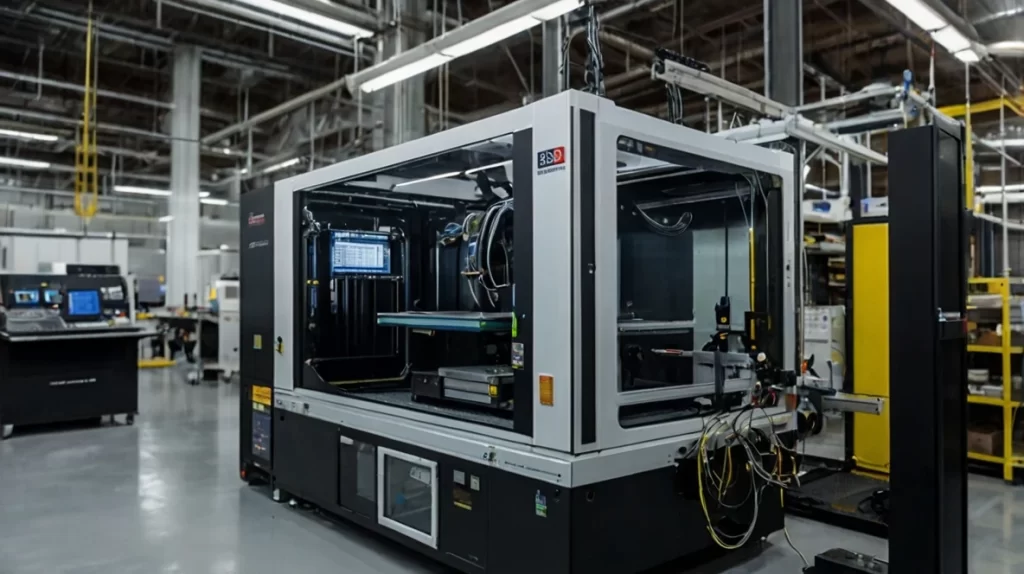
The Role of 3D Printing in Machine Customization and Maintenance
Industrial machines often require custom parts for maintenance, optimization, or automation enhancements, but sourcing these components through traditional methods can be time-consuming and expensive. With 3D printing and conductive filaments, manufacturers can:
- Fabricate machine-specific replacement parts in-house, reducing dependence on external suppliers.
- Embed conductive pathways within mechanical components, integrating sensors, switches, and connectors directly into custom-printed parts.
- Modify or improve automation systems by designing custom brackets, mounts, and housings for control modules, touch-sensitive interfaces, and IoT sensors.
By leveraging ABC3D’s high-performance conductive filaments, factories can modernize older machines, improve automation, and extend the lifespan of critical equipment without relying on expensive retrofitting or hard-to-source OEM components.
Key Applications of 3D-Printed Conductive Parts in Industrial Machines
From sensor housings and custom PCB enclosures to electrically conductive machine components, 3D-printed conductive filaments are being used across industries to improve manufacturing efficiency and automation capabilities.
1. Rapid Replacement of Machine Components
When a machine component fails or wears out, waiting for a new part from a supplier can result in costly downtime. Instead, manufacturers can 3D print conductive replacement parts on-site, ensuring quick repairs and reducing maintenance delays.
Examples include:
- Custom electrical connectors to replace worn-out PCB enclosures in industrial control panels.
- Conductive brackets and mounts for wiring and sensors, allowing for quick, modular repairs.
- ESD-safe housings for electronics, reducing static buildup in automated production lines.
2. Smart Sensor Integration for Predictive Maintenance
Many industrial machines rely on predictive maintenance sensors to monitor temperature, pressure, vibration, and electrical current. 3D printing conductive sensor housings enables factories to retrofit older equipment with real-time monitoring capabilities.
Manufacturers can embed conductive traces directly into machine components, eliminating the need for external wiring and allowing for:
- Customized pressure sensors for hydraulic systems.
- Printed capacitive touch panels for machine interfaces.
- Integrated vibration monitoring sensors to detect wear and tear before failures occur.
3. Upgrading Automation Systems with Custom Conductive Components
Automation plays a vital role in modern manufacturing, and 3D printing conductive parts allows engineers to customize and optimize automation equipment. Instead of using standard off-the-shelf parts, manufacturers can design and print parts tailored to their specific automation needs.
Applications include:
- Printed conductive actuator housings for robotic arms.
- Custom enclosures for IoT-enabled controllers in industrial automation.
- EMI shielding casings for high-voltage machinery.
These advancements provide cost savings, improved efficiency, and increased reliability across automated manufacturing lines.
Optimizing 3D Printing for Industrial Machine Components
To maximize the performance and reliability of 3D-printed conductive machine parts, it’s crucial to use the right filament, fine-tune printing parameters, and apply proper post-processing techniques.
Choosing the Right Conductive Filament for Machine Applications
The selection of conductive filament depends on the specific industrial use case:
- For rigid, high-strength components → Use conductive ABS or polycarbonate for durability and impact resistance.
- For flexible, shock-absorbing components → Conductive TPU is ideal for wearable sensors, wire guides, and dynamic machine parts.
- For EMI shielding and high-precision electronics enclosures → Carbon-loaded conductive filaments provide excellent static protection.
Fine-Tuning Print Settings for Industrial Applications
- Extrusion Temperature: Maintain 220-250°C for strong layer adhesion and electrical continuity.
- Print Speed: Slower speeds (30-40 mm/s) ensure precise conductive traces and mechanical durability.
- Layer Height & Trace Width: Using lower layer heights (~0.1 mm) improves surface detail, while wider traces (~0.6 mm) reduce electrical resistance for better conductivity.
Post-Processing to Improve Electrical Performance
- Use conductive adhesives or low-temperature soldering for improved connectivity between 3D-printed conductive parts and external electronic components.
- Smoothing techniques (such as acetone vapor finishing for ABS) can enhance contact reliability in circuits.
Why ABC3D’s Conductive Filaments Are the Best Choice for Machine Customization
At ABC3D, we offer industrial-grade conductive filaments that provide the perfect balance of durability, electrical performance, and mechanical strength. Our materials are:
- Designed for heavy-duty industrial applications, ensuring long-lasting machine performance.
- Compatible with a wide range of industrial 3D printers, making it easy to integrate into existing workflows.
- Optimized for EMI shielding, static-safe enclosures, and conductive pathways, reducing machine downtime and maintenance costs.
By using ABC3D’s specialized conductive filaments, manufacturers can extend the lifespan of industrial equipment, enhance automation systems, and streamline repair operations.
The Future of Custom 3D-Printed Industrial Machine Components
As 3D printing technology advances, industries will increasingly adopt customized conductive parts for industrial automation, predictive maintenance, and real-time monitoring. The ability to print complex electronic and mechanical parts on demand will drive greater efficiency, reduced costs, and increased operational flexibility. Future innovations in multi-material 3D printing, improved graphene-enhanced conductive filaments, and AI-driven predictive maintenance solutions will further transform how manufacturers upgrade and repair industrial machines.
At ABC3D, we are committed to pushing the boundaries of conductive 3D printing to help manufacturers, engineers, and automation experts stay ahead of the competition.
Upgrade Your Industrial Machines with ABC3D Conductive Filaments.Whether you need custom machine components, advanced sensor housings, or conductive automation parts, ABC3D’s high-performance conductive filaments offer the strength, conductivity, and durability required for heavy-duty industrial applications. Explore our range of conductive filaments today! Need assistance selecting the best filament for your project? Contact our team for expert recommendations and technical support!