In today’s competitive industrial manufacturing landscape, companies are constantly searching for ways to reduce costs, increase efficiency, and streamline production. Traditional methods for producing electronic parts, enclosures, and circuitry involve expensive materials, time-consuming processes, and significant labor costs. However, the introduction of 3D printing with conductive filaments is transforming how manufacturers approach cost-effective electronics production.At ABC3D, we provide high-performance conductive filaments designed to replace costly traditional processes, enabling manufacturers to produce custom conductive components in-house, reduce waste, and accelerate product development cycles. By leveraging 3D printing technology, companies can create functional electronic parts, conductive prototypes, and industrial-grade enclosures at a fraction of the cost of traditional manufacturing.
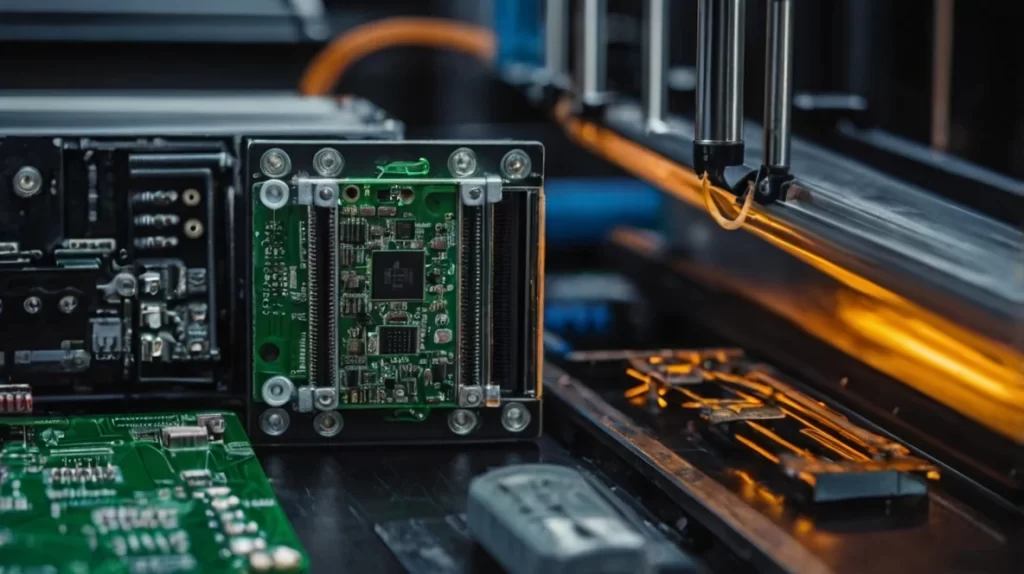
How 3D Printing with Conductive Filaments Reduces Manufacturing Costs
Traditional manufacturing methods for electronic components and conductive parts involve multiple steps, including:
- CNC machining or injection molding, which requires expensive tooling and long production lead times.
- PCB manufacturing, which involves chemical etching, plating, and multi-layer lamination, driving up costs.
- Manual assembly of wiring and circuit housings, increasing labor expenses and production time.
With 3D printing and conductive filaments, manufacturers can:
- Eliminate the need for external suppliers by producing components on-demand.
- Reduce material waste through additive manufacturing, which only uses the exact amount of material needed.
- Streamline prototyping and small-batch production, lowering R&D costs and improving iteration speed.
By integrating ABC3D’s conductive filaments, companies can transition from expensive, multi-step manufacturing processes to a more agile, cost-efficient production model.
Key Areas Where Conductive Filaments Cut Costs in Industrial Manufacturing
From electronic enclosures and circuit boards to sensor housings and EMI shielding, conductive filaments offer a lower-cost alternative to traditional metal-based or injection-molded components.
- Replacing Expensive Metal Components with Conductive Polymers
Traditionally, electronic enclosures, shielding cases, and conductive pathways are made from machined aluminum or copper, both of which are costly and require specialized processing.
By 3D printing these components with conductive filaments, manufacturers can:
- Reduce raw material costs by replacing metal with lightweight conductive polymers.
- Eliminate CNC machining expenses, which often require high setup costs and skilled labor.
- Produce customized conductive components in-house, avoiding outsourcing fees.
Industries such as automotive, aerospace, and telecommunications are already shifting toward conductive polymer-based enclosures, improving cost efficiency and design flexibility.
- Lowering PCB Production Costs with 3D-Printed Conductive Traces
Conventional PCB manufacturing involves chemical etching, plating, and multiple fabrication steps, all of which contribute to high production costs and long lead times.
With 3D-printed conductive filaments, manufacturers can:
- Print circuit traces directly onto insulating substrates, reducing reliance on etched copper boards.
- Develop custom electronic components on-demand, eliminating minimum order quantities (MOQs) required by PCB suppliers.
- Reduce waste by printing only what is needed, unlike traditional PCB production that generates excess material.
For rapid prototyping, small-batch PCB production, and IoT device development, 3D-printed conductive circuits significantly lower development and iteration expenses.
- Streamlining Prototyping & Small-Scale Manufacturing
Prototyping with traditional injection molding or outsourced fabrication can be expensive and time-consuming, with tooling costs often exceeding tens of thousands of dollars.
By switching to 3D-printed conductive filaments, companies can:
- Prototype functional electronics faster and at a lower cost, avoiding high mold tooling expenses.
- Test multiple design iterations without committing to large-scale production, improving product development efficiency.
- Customize parts for specific applications, offering more flexibility in small-batch manufacturing.
Startups, research labs, and companies in high-tech industries can leverage 3D printing to accelerate innovation while keeping costs low.
Optimizing Conductive Filament Printing for Cost Savings
To maximize cost efficiency, manufacturers must optimize their printing parameters, material selection, and production workflow. ABC3D’s conductive filaments are designed for industrial applications, ensuring high electrical performance and mechanical strength while keeping production costs under control.
Best Practices for Reducing Costs with Conductive 3D Printing
- Choose the Right Conductive Filament for Your Application:
- For structural electronic enclosures: Carbon-filled conductive ABS or polycarbonate provides high durability.
- For printed circuit traces and PCB replacements: Graphene-infused conductive filaments improve signal transmission.
- For flexible, wearable applications: Conductive TPU allows for stretchable, dynamic circuitry.
- Optimize Print Settings to Minimize Material Waste:
- Extrusion Temperature: Maintain 220-250°C for consistent conductivity and strong layer bonding.
- Print Speed: Use 30-40 mm/s to prevent defects and minimize filament waste.
- Layer Height & Line Width: Adjust layer height (~0.1 mm) for fine circuit details, while increasing trace width (~0.6 mm) for better electrical flow.
- Integrate Smart Post-Processing Techniques to Enhance Conductivity:
- Use conductive adhesives or soldering techniques to improve electrical connections between 3D-printed components.
- Apply surface treatments (e.g., conductive coatings) to increase circuit efficiency, reducing the need for additional material layers.
- By implementing these techniques, manufacturers can further reduce costs and improve performance in industrial 3D printing applications.
Why ABC3D’s Conductive Filaments Are the Best Choice for Cost-Effective Manufacturing
At ABC3D, we offer advanced conductive filaments that enable manufacturers to reduce costs while maintaining high-performance standards. Our materials are:
- Affordable & Scalable: Designed to replace expensive metal components and PCB manufacturing.
- Durable & Industry-Tested: Withstand high-stress environments, ensuring reliable performance in industrial applications.
- Versatile & Customizable: Available in multiple polymer bases to suit various manufacturing needs.
As industrial 3D printing adoption grows, companies will continue to explore ways to cut costs, minimize waste, and increase production efficiency. Future advancements in multi-material conductive printing, AI-driven manufacturing optimization, and enhanced conductive polymers will further drive cost savings and innovation. With ABC3D leading the way, manufacturers can embrace affordable, scalable, and high-performance conductive 3D printing solutions, ensuring a more flexible and cost-efficient production model.
If you’re looking to reduce costs in industrial electronics production, prototype faster, and improve manufacturing efficiency, ABC3D’s conductive filaments provide the perfect solution.